
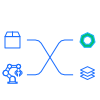
Integrated Across All Areas
Connected to the company's programs and devices for instant data exchange. Facilitating management for supervisors and operators.
Integrates all areas of the company.
Connected to any ERP and other programs; Connected to machine signals; Real-time data reception in a paperless environment.
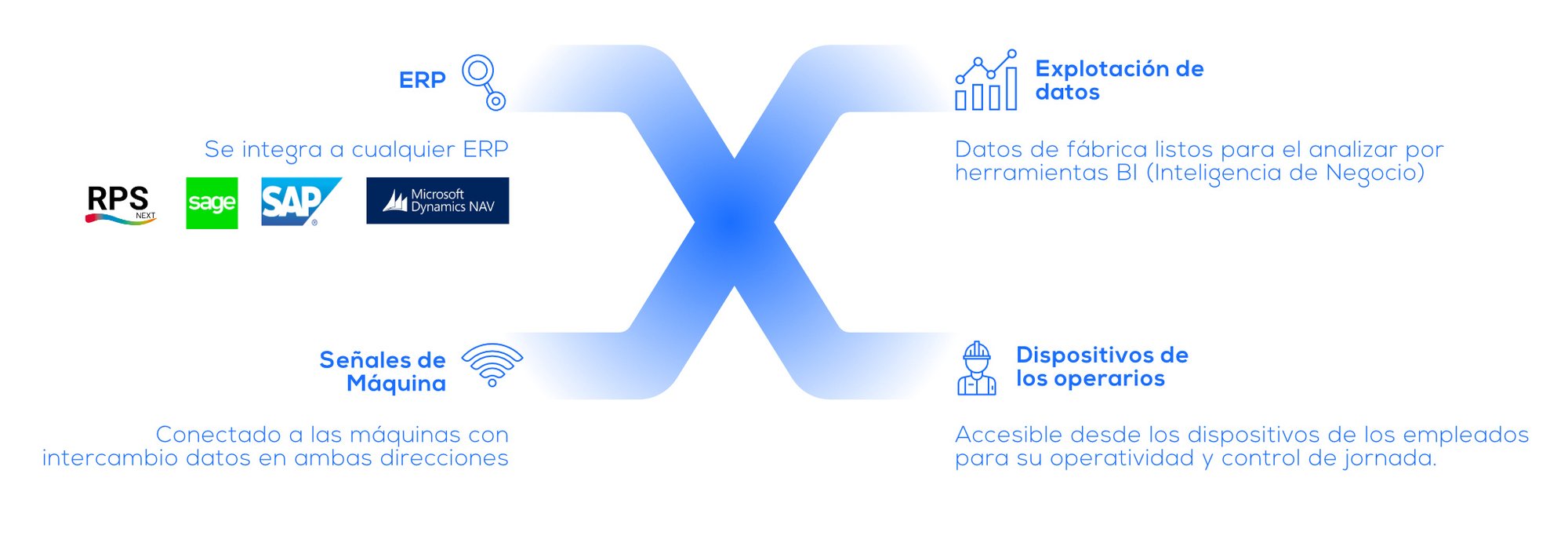
Perfectly Designed IT Architecture
- MES system network designed for efficient connectivity.
- Connected to the company's network.
- Bidirectional digital data exchange that streamlines work.
- Automatic data logging through sensors, cameras, robots.
Detailed Functionalities
Basic Records:
- Basic record structures (materials, resources, work orders, etc.).
- Complete user configuration, local or web-connected user group definitions, and interaction rule definitions.
- Complete menu, panel, list, icon configuration.
- Multilingual and multi-plant management based on user profiles.
- Shift and calendar management.
- Sending local or distributed information: orders, operations, materials, resources, drawings, notes, files in any format (Word, Excel, DXF, etc.).
- Batch and split operations.
- Real-time production plan progress and monitoring:
- Production progress status and management.
- Parametric controls of declared quantities.
- Visibility of the activity queue.
- Parametric control of production sequence: production progress control rules, moving sequences.
- Milestone (automatic progress rollback for orders).
- Definition of milestone operations.
- Automatic progress of milestone operations.
- Automatic progress of previous operations.
- Quantity leveling and backflush and milestone propagation in balancing and time rules for "non-milestone" operations.
- Alternative resource and operation management: management of multi-element work orders.
- Storage of multiple items in the warehouse: storing the same material in different batches.
- Time progress and balancing (real-time):
- Standard setup and working time configuration for machinery and labor.
- Collect real-time setup/work/rework times for machinery and labor.
- Subdivision of indirect time, justified downtime, maintenance, etc.
- Additional compensation/authorization time.
- Printing of plant documentation (work order, task, picking list) for operational support.
- Resource monitoring.
- Real-time monitoring control panel.
- Resource status indicator (working/setup, available, blocked).
- Display of logical states, ongoing activities, active operators.
- Display of pending queue.
- List of historical "event logs" for operations and resources.
- Graphical dashboard function for machine statuses.
- Machine stop button with block type causation (also in deferred mode).
- Automatic task suspension and reopening, automatic storage and collection.
- Operator skill management.
- Integration with external attendance/payroll management systems.
- Ability to modify acquired declarations or add new ones to balance times and quantities.
Frequently Asked Questions
How will it benefit my company?
INEXION MES makes it possible to automate and control all processes involved in the manufacturing of your products, significantly improving plant productivity and performance.
Who performs the implementation?
A team from Overtel is responsible for the entire process, from customer contact to on-site implementation, training, and development. For this, a Coordinator, Project Director, Implementer, and Developer are assigned, working together to ensure a successful implementation.
How long does it take?
The INEXION MES system can take approximately 2 to 3 months, but this duration may vary depending on specific case characteristics. You can book a demo to discuss your specific case
Will it adapt to my production plant?
Yes, it's a system adaptable to any type of industrial plant. Ask one of our consultants, and they will provide more specific information about your case.